“We Don’t Want to Live Without It”
How the Renegade TMB 8100 Parts Washer Transformed MI Windows and Doors Operations
MI Windows and Doors was established in the 1940s and is a leading manufacturer of high-quality, energy-efficient residential windows and doors.
MI Windows and Doors has a long-standing reputation for producing precision-engineered windows and doors. But behind the scenes, the company was grappling with inefficiencies in its parts-cleaning process—until they found a solution in Renegade’s TMB 8100 Stretch Flush-Through Parts Washer.
In September 2024, MI shared their experience with the Renegade Parts Washer that was added to their Profiles Manufacturing facility. They also discussed what it was like to partner with Renegade to solve their cleaning challenges.
Company Overview:
- Company Name: MI Windows and Doors
- Industry: Window and Door Manufacturing
- Location: Millersburg, PA
- Service Area: Eastern United States
Case Study Featuring:
- Chris Herb Jr., Die Shop Supervisor
- Andy Adams, Manager
- Jeff Fetterhoff, Die Cleaner
- James Starr, CI Specialist
The Need for a Solution
Inefficient, Labor-Intensive Manual Cleaning
Before partnering with Renegade, MI was bogged down by a labor-intensive and time-consuming manual cleaning process. Tools and molds had to be disassembled, scrubbed by hand, and reassembled—a task that often took 3 to 4+ hours per tool.
“Our biggest challenge was the time and labor it took to manually clean parts. At peak production time, we were cleaning 40 or more a week, making it a challenge to keep up and not delay production,” said Chris Herb Jr., Die Shop Supervisor.
Jokingly Jeff Fetterhoff, Die Cleaner stated, “Yeah, I am a little disappointed because we don’t have overtime anymore.”
Not only was the process time-consuming, but it also posed safety risks and increased wear on equipment.
- The work area conditions “became unsafe, too. Our tables were filled with units, and the racks were overflowing. We had tooling everywhere, waiting to be cleaned,” said Andy Adams, Manager.
- As Jeff explained, “We had to take everything apart—every bolt—scrub it, and put it back together. It was tedious, exhausting, and took a toll on our equipment.”
Selecting Renegade
A Collaborative Approach to Customization
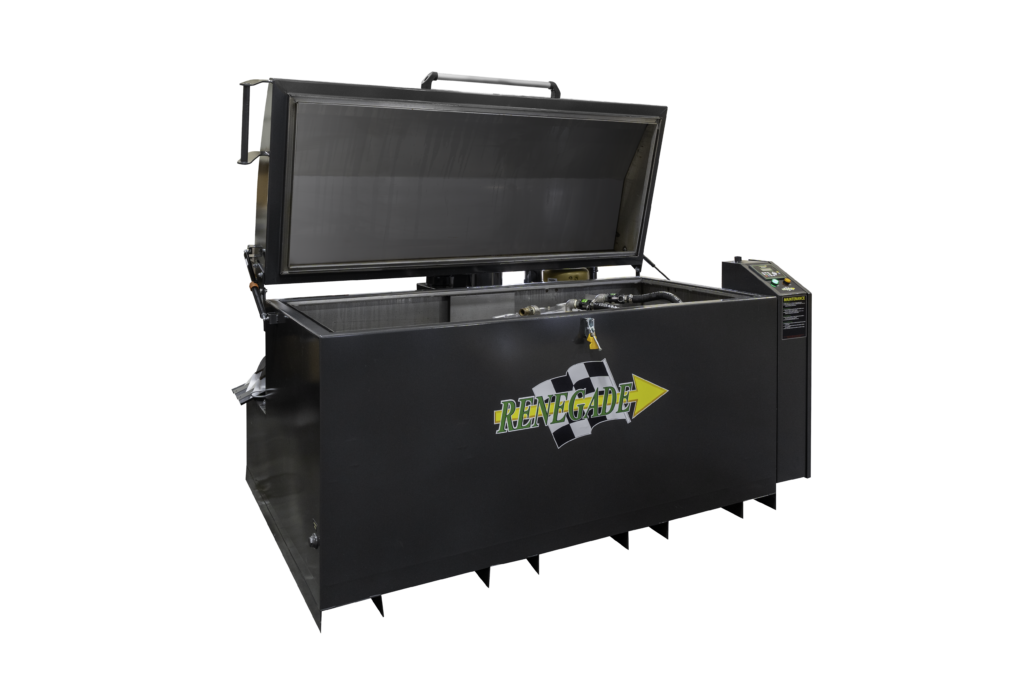
MI first heard about Renegade through online research. After seeing other industries successfully use Renegade’s parts washers, MI Profiles reached out to explore how the technology could address their needs.
“Our business case was hard at the time as we had to convince the financial department that this was going to do something for us,” stated Andy, who eventually got approval and worked with Renegade to implement an automatic parts washer.
Chris recalled that Derek Tylka, Renegade Project Manager “worked with us to understand our process and cleaning needs. He didn’t just try to sell us what they already had; Renegade customized a solution for us.”
The Renegade team didn’t stop at just understanding MI’s cleaning needs, they “worked with us to customize the machine and throughout the stages of design, they kept checking in, showing us their progress, and ensuring it met our requirements.”
“Their engineers were great to work with!” said Chris.
Test Washing Experience
“We sent one of our units out there, and they hooked it up. It was a clean unit, and Renegade was able to push dirt out of it, which was really amazing. To us, that unit would have been clean, and we would have never known!”
Implementation
Immediate Impact
The setup was seamless. “When we received the unit, it worked even before we had training on it,” said Andy. “The design was spot on.”
“Derek came out and helped us make final adjustments,” noted Andy. “It was excellent support from start to finish.”
Timing:
- Started the conversation with Renegade Aug of 2023
- Purchased Feb of 2024
- Test wash and engineering approvals
- Shipped June 6, 2024
- Implemented June 2024
Results
Huge Reduction in Cleaning Time
Since implementing the Renegade TMB 8100 Flush-Through Parts Washer, MI Profiles has seen significant improvements in its operations:
- Increased capacity and production efficiency: “What used to take us three days now takes just one shift. We can get so much more done,” explained Chris.
- Improved cleanliness: The team realized that previously they were cleaning the main unit of the tool but now the parts washer cleans all hoses and fittings as well. “The quality of cleaning is far superior to what we could do by hand. Every chamber and pocket is now cleaned 100%.”
- Safer work environment and reduced labor strain: “Before, we were handling harsh solvents and breaking down equipment by hand. Now, the washer does all the work,” said Andy.
- Safer and easier on employees: “The machine not only improved cleaning speed but also led to safer working conditions. “We don’t have to deal with solvents anymore, and the automatic cleaning has really improved the ease on employees,” said Jeff.
- Better Monday Mornings: Andy said, “we use to come in on Monday mornings and dread to see what we had to clean.” Now they see empty shelves and don’t have that feeling.
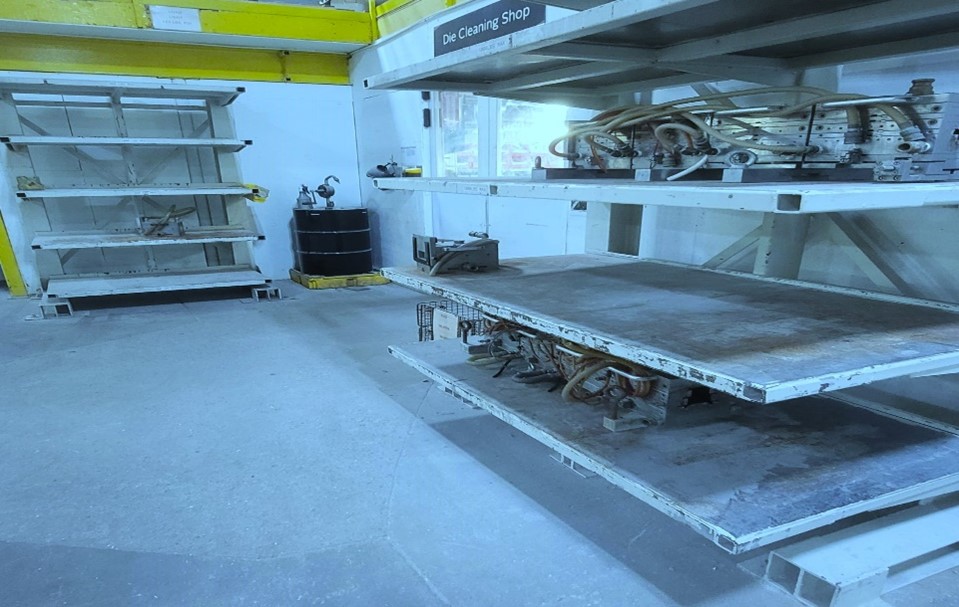
PLUS now employees can work on other tasks: “Before the washer, cleaning sucked up all our time. We couldn’t get other things done, like maintaining our other units or inserters. But now, we have time to handle those tasks, which has a huge impact on production” stated Andy.
Before and After
Key Aspect | Before Using the Renegade Washer | After Using the Renegade Washer |
---|---|---|
Time | 3-4+ hours to clean one tool | 75% reduction—cleaning now takes one shift |
Labor Demands | Labor-intensive manual cleaning | Minimal manual intervention—set and go |
Cleaning Quality | Inconsistent, incomplete cleaning | 100% of the parts are now cleaned thoroughly |
Work Area | Shelves full of tools awaiting cleaning | Empty shelves and clear workspaces |
Safety | Chemical-heavy process | No solvents, safer work environment |
Satisfaction
Meeting and Exceeding Expectations
“I was skeptical at first, but once we saw how clean everything came out, I was sold,” stated Jeff. He added “we don’t want to live without it. The Renegade washer delivered on everything it promised and more.”
Andy reflected on his efforts to get this equipment approved in the “hopes that it will help the department.” The washer’s efficiency has turned quickly it into “a critical piece of our department, and we’re going to take good care of it because we don’t want to be without it.”
Chris Herb Jr., Die Shop Supervisor added that “it is one of the rare pieces of equipment that actually lives up to its promises. It cleaned our worst tools better than we could have imagined.”
Renegade’s Sump Sweep and Filtration System:
After a month of hard running, the team drained the system to learn how to maintain the machine, “we all had the assumption that all that gunk and stuff has got to be in the tank”, but when it was drained – it was spotless.
The bottom of the tank was as clean as when it was shipped to us” Andy said about the effectiveness of the sump sweep and filtration system.
Conclusion
A Game-Changer for MI Profiles Brands
The Renegade TMB 8100 Stretch Flush-Through Parts Washer has revolutionized the operations at MI Windows and Doors. By automating a labor-intensive and time-consuming task, they’ve freed up valuable labor, increased their production capacity, and improved the cleanliness and lifespan of their tools.
“We don’t want to live without it. Everything Renegade said it would be, it is,” said Jeff.
Would You Recommend Renegade?
“Absolutely. Renegade delivered everything they said it would, and we’d recommend them to anyone,” said the team!